2.3. таблица решений по определению приоритетности товаров
2.3. таблица решений по определению приоритетности товаров
для производства
С учётом значимости функций продукции, её комплектующих и уровня затрат посредством ценообразования, основываясь на знании спроса на продукцию, определяется уровень её рентабельности. Всё это в совокупности служит основой для принятия решения о выборе конкретного товара к производству или направлений и масштаба его усовершенствования.
Проблема конкуренции с продукцией фирм Японии и США становится всё более острой не только для европейских фирм, но и для российских. Например, отечественная телевизионная промышленность практически проиграла битву за потребителя, та же участь грозит автомобильной промышленности, да и многим другим отраслям. А остриём этой конкурентной борьбы являются:
повышение эффективности производства, в частности, снижение затрат на разработку качественной конкурентной продукции;
ориентация всех стадий производственного процесса, начиная от разработки на удовлетворение потребителей;
повышение деловой культуры и улучшение управления во всех звеньях производства.
Для того чтобы выполнить эти требования, нужно использовать новую технологию разработки, планирования и технической подготовки производства изделий. Такая технология разрабатывалась в Японии начиная с конца 1960-х гг. (с 1966 г.) и сейчас всё шире используется в разных странах мира. Одним из основных инструментов этой технологии является метод QFD (Quality Function Deploement) — развёртывание функций качества [12]. Это экспертный метод, использующий табличный способ представления данных, причём со специфической формой таблиц, которые получили название «домиков качества».
Основная идея технологии QFD заключается в том, что между потребительскими свойствами («фактическими показателями качества» по терминологии К. Исикавы) и нормируемыми в стандартах, технических условиях параметрами продукта («вспомогательными показателями качества» по терминологии К. Исикавы) существует большое различие. Например, одним из потребительских свойств микропровода может быть «отсутствие обрывов при намотке катушек индуктивности на специальном станке». Это фактический показатель качества микропровода. Чтобы обеспечить этот фактический показатель, производитель использует такие параметры, как предел прочности материала микропровода на разрыв, диаметр, параметры шероховатости поверхности, микротвёрдость и т.д. Это вспомогательные показатели качества, которые важны для производителя, но не всегда существенны для потребителя. В идеальном случае производитель мог проконтролировать качество продукции непосредственно по фактическим показателям, но это, как правило, невозможно, поэтому он пользуется вспомогательными показателями.
Технология QFD — это последовательность действий производителя по преобразованию фактических показателей качества товара в технические требования к продукции, процессам и оборудованию.
Основным инструментом технологии QFD является таблица специального
вида, получившая название «домик качества». В этой таблице удобно отображать связь между фактическими показателями качества (потребительскими
свойствами) и вспомогательными показателями (техническими требованиями). Основные этапы технологии QFD включают (рис. 2.5) [12]:
1) разработку плана качества и проекта качества. На этом этапе проводится исследование состояния рынка и запросов потребителей, устанавливается, что следует производить. С учётом других важных параметров рынка разрабатывается таблица требований потребителей к качеству. Устанавливаются основные
требования и маркетинговые параметры продукции. Анализируются и оцениваются изделия конкурентов. На этой основе составляется план по качеству, в котором отражаются маркетинговые рейтинги разрабатываемого изделия. Определяется важность (рейтинг) каждого из установленных требований по качеству. Определяются компоненты изделия, на основании анализа продукции конкурентов устанавливаются технические параметры компонентов, исследуются рекламации и замечания потребителей по качеству.
І Іл-ан ьэ'+астЕ продукта
![]() |
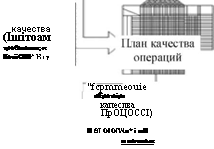
![]() |
параметры качества
(технические требования)
компонента
Критические
параметры качества процесса изготовления
и контроля
Рабочие инструкции для процесса изготовления, сборки, контроля и испытаний продукции
Рис. 2.5. Схема процесса QFD
Исследуются фактические параметры качества и преобразуются во вспомогательные параметры качества компонентов. На этой основе разрабатывается план по качеству. Устанавливаются методы обеспечения качества и испытаний продукта и элементов;
разработку детализированного проекта качества и подготовку производства. На данном этапе параметры качества конечного продукта преобразуются в параметры качества узлов, которые заносятся в специальные таблицы для элементов и отдельные таблицы для узлов и сборочных единиц (в которые входят таблицы для отдельных элементов). Окончательно устанавливаются функции элементов и узлов изделия, а также признаки качества узлов и стандарты, их определяющие, планируются позиции контроля элементов и узлов изделия в будущем производственном процессе;
разработку техпроцессов. На этом этапе разрабатываются техпроцессы и технологические приспособления. При этом для каждого техпроцесса обычно проводится ФСА. На основе результатов анализа вырабатывается план процесса производства, который реализует заданную точность при минимальных затратах. Утверждаются стандарты по качеству узлов, стандарты на испытания и стандарты на покупные изделия, выбираются поставщики и устанавливаются стандарты на закупки.
Осуществляется выбор оборудования, и для каждого технологического модуля окончательно устанавливается позиция контроля качества, прежде всего для таких характеристик, как форма, размеры и прочностные параметры продукции. Определяются факторы производственного процесса, влияющие на эти характеристики качества. При этом разрабатывается таблица, в которой сопоставляются признаки качества конечного продукта и признаки качества и условия работы оборудования. Разрабатываются операционные карты технического контроля и таблица качества для окончательной сборки изделия. После выбора средств контроля разрабатывается система технического контроля в сборочном производстве для выбранных позиций контроля.
Проводится БМЕЛ-анализ производственного процесса, методика проведения которого представлена далее. При этом анализируются как проектные данные, так и данные исследований, данные производства аналога, данные изготовления опытного образца. Все выявленные проблемы немедленно передаются в соответствующие отделы для принятия решения. Производится уточнение модели качества (отражённой в таблицах) и корректировка проекта.
Такая технология работы позволяет учитывать требования потребителя на всех стадиях производства изделий, для всех элементов качества предприятия и, таким образом, резко повысить степень удовлетворённости потребителя, снизить затраты на проектирование и подготовку производства изделий.
В современных условиях хозяйствования процесс принятия управленческих решений тактического и стратегического характера базируется на информации о затратах и финансовых результатах деятельности предприятия. Одним из эффективных инструментов в управлении затратами предприятия является система учёта стандарт-кост, в основе которой лежит принцип учёта и контроля затрат в пределах установленных норм и нормативов и по отклонениям от них [6].
Метод нормативного определения затрат возник в начале XX в. в США. Это был один из принципов научного менеджмента, предложенных Ф. Тейлором, Г. Эмерсоном и другими инженерами, которые дали толчок развитию системы нормативного учёта затрат. Они применяли стандарты, чтобы выявить «единственный наилучший путь» использования труда и материалов. Стандарты обеспечивали информацией для планирования хода работ так, что потребление материалов и труда сводилось к минимуму.
Впервые полную действующую систему нормативного определения затрат в 1911 г. разработал и внедрил в США Ч. Гаррисон. Идея стандарт-коста у Ч. Гаррисона трансформировалась в два положения:
все произведённые затраты в учёте должны быть соотнесены со стандартами;
отклонения, выявленные при сравнении фактических затрат со стандартами, должны быть расчленены по причинам.
Со времени своего возникновения система учёта стандарт-кост успешно развивалась и сейчас широко используется многими ведущими фирмами стран с развитой рыночной экономикой.
Термин стандарт-кост состоит из двух слов: «стандарт», который означает количество необходимых производственных затрат (материальных и трудовых) для выпуска единицы продукции или заранее исчисленные затраты на производство единицы продукции или оказания услуг, а слово «кост» это затраты, приходящиеся на единицу продукции. Таким образом, стандарт-кост в полном смысле слова означает затраты по стандарту. Эта система направлена прежде всего на контроль за использованием прямых издержек производства, а смежные калькуляции для контроля накладных расходов.
Система стандарт-кост удовлетворяет запросы производителей и служит мощным инструментом для контроля производственных затрат. На основе установленных стандартов можно заранее определить сумму ожидаемых затрат на производство и реализацию изделий, исчислить себестоимость единицы изделия для определения цен, а также составить отчёт об ожидаемых доходах будущего года. При этой системе информация об имеющихся отклонениях используется руководством для принятия оперативных управленческих решений.
В основе системы стандарт-кост лежит предварительное (до начала производственного процесса) нормирование затрат по статьям расходов:
основные материалы;
оплата труда основных производственных рабочих;
производственные накладные расходы (заработная плата вспомогательных рабочих, вспомогательные материалы, арендная плата, амортизация оборудования и др.);
коммерческие расходы (расходы по сбыту, реализации продукции).
Предварительно исчисленные нормы рассматриваются как твёрдо установленные ставки, с тем чтобы привести фактические затраты в соответствие со стандартами путём умелого руководства предприятием. При возникновении отклонений стандартные нормы не изменяют, они остаются относительно постоянными на весь установленный период, за исключением серьёзных изменений, вызываемых новыми экономическими условиями, значительным повышением или снижением стоимости материалов, рабочей силы или изменением условий и методов производства. Отклонения между действительными и предполагаемыми затратами, возникающие в каждом отчётном периоде, в течение года накапливаются на отдельных счетах отклонений и полностью списываются не на затраты производства, а непосредственно на финансовые результаты предприятия.
Схематически система учёта стандарт-кост выглядит следующим образом.
Выручка от продажи продукции.
Стандартная себестоимость продукции.
Валовая прибыль (п. 1 п. 2).
Отклонения от стандартов.
Фактическая прибыль (п. 3 п. 4).
Калькуляция, рассчитанная при помощи стандартных норм, является основой оперативного управления производством и затратами. Выявляемые в текущем порядке отклонения от установленных стандартных норм затрат подвергаются анализу для выяснения причин их возникновения. Это позволяет администрации оперативно устранять неполадки в производстве, принимать меры для их предотвращения в будущем.
Следует отметить, что система стандарт-кост в зарубежной практике не регламентирована нормативными актами, в связи с чем не имеет единой методики установления стандартов и ведения учётных регистров. Даже внутри одной компании действуют различные нормы: базисные, текущие, идеальные, прогнозные, достижимые и облегчённые.
При установлении норм широко используются физические (количественные) стандарты, позволяющие измерить в натуральном выражении расход материала, количество рабочей силы и объём услуг, необходимых для производства данного изделия. Эти физические стандарты затем умножают на коэффициенты в денежном исчислении и получают стандартные стоимостные нормы.
В связи с тем что накладные расходы охватывают множество отдельных статей, часть которых трудно или нецелесообразно измерять точно, стандарты накладных расходов даются в денежной оценке без указания количественных норм. Исключение составляют важнейшие составные части накладных расходов (например, непроизводственная заработная плата), по которым в некоторых случаях могут устанавливаться количественные стандарты.
В условиях рыночной экономики цены на материалы подвержены непрерывным колебаниям в зависимости от спроса и предложений. Поэтому стандарты на материалы устанавливаются большей частью либо исходя из уровня цен, которые действуют в момент разработки стандартов, либо исходя из определения средних цен, которые будут преобладать в течение периода использования норм. Соответственно стандарты ставок заработной платы по операциям технологического процесса часто являются средними расценками.
Нормы расхода материалов и производственной заработной платы устанавливаются обычно в расчёте на одно изделие. Для контроля за накладными расходами разрабатываются сметные ставки за определённый период, исходя из намеченного объёма продукции. Сметы накладных расходов носят постоянный характер. Однако при колебаниях объёма производства для контроля за накладными расходами создаются переменные стандарты и скользящие сметы.
В основе установления скользящих смет накладных расходов лежит классификация затрат в зависимости от величины объёма выпуска на постоянные, переменные и полупеременные. Последние, в свою очередь, разбиваются на постоянные и переменные составные элементы. В результате сметная ставка (норма) накладных расходов определяется как сумма переменной их части по заранее установленным нормам на единицу объёма выпуска и постоянных издержек.
Для исчисления стандартной себестоимости продукции нормативные затраты на материалы, рабочую силу и накладные расходы суммируются.
На предприятиях, применяющих систему учёта стандарт-кост, учёт отклонений фактических расходов от стандартных норм ведут, как правило, на следующих счетах.
«Отклонения по расходу материалов».
«Отклонения по заработной плате».
«Отклонения по накладным расходам».
«Отклонения от стандартной коммерческой себестоимости».
При необходимости (например, при отражении отклонений с подразделением по причинам) каждый из этих счетов может быть расчленён на более мелкие аналитические счета.
Главное в стандарт-косте — контроль за наиболее точным выявлением отклонений от установленных стандартов затрат, что способствует совершенствованию и самих стандартов затрат. При отсутствии же такого контроля применение стандарт-коста будет иметь условный характер и не даст надлежащего эффекта.
Принципы этой системы являются универсальными, поэтому их применение целесообразно при любом методе учёта затрат и способе калькулирования себестоимости продукции.
Вместе с тем этой системе присущи свои недостатки. На практике очень трудно составить стандарты согласно технологической карте производства. Изменение цен, вызванное конкурентной борьбой за рынки сбыта товаров, а также инфляцией, осложняет исчисление стоимости остатков готовых изделий на складе и незавершённого производства. Стандарты можно устанавливать не на все производственные затраты, в связи с чем на местах всегда ослабляется контроль за ними. Более того, при выполнении производственной компанией большого количества различных по характеру и типу заказов за сравнительно короткое время исчислять стандарт на каждый заказ практически невозможно. В таких случаях вместо научно обоснованных стандартов на каждое изделие устанавливают среднюю стоимость, которая является базисом для определения цен на изделие.
Несмотря на эти недостатки, руководители фирм и компаний используют систему учёта стандарт-кост как мощный инструмент контроля за издержками производства и калькулирования себестоимости продукции, а также для управления, планирования и принятия необходимых управленческих, технических, организационных и других решений.
Обобщая вышеизложенное, можно сделать вывод, что нормативный метод учёта затрат и система стандарт-кост не являются тождественными понятиями. Однако идея обеих систем едина — установление нормативов (стандартов), выявление и учёт отклонений с целью обнаружения и устранения проблем в производстве и реализации продукции. В настоящее время происходит процесс реформирования отечественной системы бухгалтерского учёта. Она всё больше стала соответствовать требованиям рыночной экономики и международным стандартам финансовой отчётности.
Достаточно широко используется метод анализа затрат на качество — FMEA-анализ (Failure Mode and Effects Analysis). FMEA-анализ представляет собой технологию анализа возможности возникновения дефектов и их влияния на потребителя. FMEA-анализ проводится для разрабатываемых товаров и процессов с целью снижения риска потребителя от потенциальных дефектов.
FMEA-анализ в настоящее время является одной из стандартных технологий анализа качества изделий и процессов, поэтому в процессе его развития выработаны типовые формы представления результатов анализа и правила его проведения.
Данный вид функционального анализа используется как в комбинации с функционально-стоимостным и функционально-физическим анализом, так и самостоятельно. Он позволяет снизить затраты и уменьшить риск возникновения дефектов.
FMEA-анализ в отличие от ФСА не только анализирует прямо экономические показатели, в том числе затраты на недостаточно высокое качество, а позволяет выявить именно те дефекты, которые обусловливают наибольший риск потребителя, определить их потенциальные причины и выработать корректирующие действия по их устранению ещё до того, как эти дефекты проявятся, и таким образом предупредить затраты на их исправление.
Обычно FMEA-анализ проводится для новой продукции или процесса. FMEA-анализ процессов может проводиться для.
процесса производства продукции;
процесса эксплуатации товара потребителем.
FMEA-анализ процесса производства обычно проводится у изготовителя ответственными службами планирования производства, обеспечения качества или производства с участием соответствующих специализированных отделов изготовителя и при необходимости потребителя. Проведение FMEA-анализа процесса производства начинается на стадии технической подготовки производства и заканчивается своевременно до монтажа производственного оборудования. Целью FMEA-анализа процесса производства является обеспечение выполнения всех требований по качеству процесса производства и сборки путём внесения изменений в план процесса для технологических действий с повышенным риском.
FMEA-анализ бизнес-процессов обычно производится в подразделениях, выполняющих данный бизнес-процесс. В проведении анализа, кроме представителей этих подразделений, принимают участие представители службы обеспечения качества, представители подразделений, являющихся внутренними потребителями результатов бизнес-процесса и подразделений, участвующих в выполнении этапов бизнес-процесса. Целью этого вида анализа является обеспечение качества выполнения запланированного бизнес-процесса. Выявленные в ходе анализа потенциальные причины дефектов и несоответствий позволят определить причину неустойчивости системы. Выработанные корректирующие мероприятия должны обязательно предусматривать внедрение статистических методов, в первую очередь для тех операций, где выявлен повышенный риск.
Этапы проведения FMEA -анализа.
Построение компонентной, структурной, функциональной и потоковой моделей объекта анализа.
Если FMEA-анализ проводится совместно с функционально-стоимостным и функционально-физическим анализом, используются ранее построенные модели.
Исследование моделей.
В ходе исследования моделей определяются.
потенциальные дефекты для каждого из элементов компонентной модели объекта.
Такие дефекты обычно связаны или с отказом функционального элемента (его разрушением, поломкой и т.д.), с неправильным выполнением элементом его полезных функций (отказом по точности, производительности и т.д.) или с вредными функциями элемента.
В качестве первого шага рекомендуется перепроверка предыдущего FMEA-анализа или анализ проблем, возникших за время гарантийного срока. Необходимо также рассматривать потенциальные дефекты, которые могут возникнуть при транспортировке, хранении, а также при изменении внешних условий (влажность, давление, температура);
потенциальные причины дефектов.
Для их выявления могут быть использованы диаграммы Исикавы, которые строятся для каждой из функций объекта, связанных с появлением дефектов;
потенциальные последствия дефектов для потребителя.
Поскольку каждый из рассматриваемых дефектов может вызвать цепочку отказов в объекте, при анализе последствий используются структурная и потоковая модели объекта;
возможности контроля появления дефектов.
Определяется, может ли дефект быть выявленным до наступления последствий в результате предусмотренных в объекте мер по контролю, диагностике и др.
Проводится ряд экспертных оценок; определяются следующие параметры.
а) параметр тяжести последствий для потребителя (проставляется обычно
по 10 балльной шкале; наивысший балл проставляется для случаев, когда последствия дефекта влекут юридическую ответственность);
б) параметр частоты возникновения дефекта (проставляется по
10 балльной шкале; наивысший балл проставляется, когда оценка частоты возникновения составляет 1/4 и выше);
в) параметр вероятности необнаружения дефекта (является 10-балльной экспертной оценкой; наивысший балл проставляется для «скрытых» дефектов, которые не могут быть выявлены до наступления последствий);
г) параметр риска потребителя (показывает, в каких отношениях друг к другу в настоящее время находятся причины возникновения дефектов; дефекты с
наибольшим коэффициентом приоритета риска подлежат устранению в первую
очередь).
Результаты анализа заносятся в специальную таблицу. Выявленные «проблемные места» подвергаются изменениям, т.е. разрабатываются корректирующие мероприятия.
Часто разработанные мероприятия заносятся в последующую графу таблицы FMEA-анализа. Затем пересчитывается потенциальный риск после проведения корректировочных мероприятий. Если не удалось его снизить до приемлемых пределов, разрабатываются дополнительные корректирующие мероприятия и повторяются предыдущие шаги.
По результатам анализа для разработанных корректирующих мероприятий составляется план их внедрения. Для этого определяется:
в какой временной последовательности следует внедрять эти мероприятия и сколько времени потребуется на проведение каждого мероприятия, через сколько времени после начала его проведения проявится запланированный эффект;
кто будет отвечать за проведение каждого из этих мероприятий и кто будет конкретным его исполнителем;
где (в каком структурном подразделении) мероприятия должны быть проведены;
из какого источника будет производиться финансирование проведения мероприятия.
Таким образом, FMEA-анализ позволяет проанализировать возможности возникновения дефектов, а также выявить степень их влияния на потребителей.
Функционально-физический анализ (ФФА) был создан в 70-е гг. прошлого столетия в результате работ, параллельно проводившихся учёными Германии и СССР.
Целью ФФА является анализ физических принципов действия, а также технических и физических противоречий в технических объектах для того, чтобы оценить качество принятых технических решений и предложить новые. При этом широко используются:
эвристические приёмы, т.е. обобщённые правила изменения структуры и свойств технических объектов;
анализ следствий из общих законов и частных закономерностей развития технических объектов; эти законы применительно к различным отраслям промышленности установлены работами отечественных учёных;
синтез цепочек физических эффектов для получения новых физических принципов действия технических объектов; в настоящее время существуют программные продукты, автоматизирующие данный процесс.
Обычно функционально-физический анализ проводится в следующей последовательности.
Формулировка проблемы.
Для этого могут быть использованы результаты функционально-стоимостного анализа или FMEA-анализа. Описание проблемы должно включать назначение технического объекта, условия его функционирования и технические требования к нему.
Составление описания функций назначения технического объекта. Описание базируется на анализе запросов потребителя и должно содержать
чёткую и краткую характеристику технического объекта, с помощью которой можно удовлетворить возникшую потребность. Описание функций технического объекта включает:
действия, выполняемые им;
объект, на который направлено действие;
условия работы технического объекта на всех стадиях его жизненного цикла.
К надсистеме относится внешняя среда, в которой функционирует и с которой взаимодействует рассматриваемый объект. Анализ надсистемы производится с помощью структурной и потоковой модели технического объекта.
Составление списка технических требований к объекту.
Данный список должен базироваться на анализе требований потребителей; на этой стадии целесообразно использовать приёмы описанной технологии развёртывания функций качества (QFD).
Построение функциональной модели технического объекта (обычно в виде функционально-логической схемы).
Анализ физических принципов действия функций технического объекта.
Определение технических и физических противоречий для функций технического объекта.
Такие противоречия возникают между техническими параметрами объекта при попытке одновременно удовлетворить несколько требований потребителя.
Определение способов разрешения противоречий и направления совершенствования технического объекта.
Для того чтобы реализовать совокупность потребительских свойств объекта, отраженных в его функциональной модели, модель преобразуется в функционально-идеальную; поиск вариантов технических решений часто производят с помощью морфологических таблиц.
8. Построение графиков, эквивалентных схем, математических моделей
технического объекта.
Важно, чтобы модель была продуктивной, т.е. позволяла найти новые возможные решения. К формированию морфологической таблицы целесообразно приступить тогда, когда появится несколько предлагаемых решений для различных функциональных элементов технического объекта.
Применение ФФА позволяет повысить качество проектных решений, создавать в короткие сроки высокоэффективные образцы техники и технологий и таким образом обеспечивать конкурентное преимущество организации.
В современных условиях деятельность отечественных производителей должна быть ориентирована на выпуск высококачественной и конкурентоспособной продукции при максимальном снижении затрат на её производство. Поэтому особую значимость приобретает использование передовых форм и методов организации труда и управления производством, применяемых в экономически развитых странах. В этой связи особый интерес представляет метод управления производством по системе JIT («just-in-time», т.е. «точно в срок»).
Система ЛТ зародилась в Японии в середине 70-х гг. XX в. в компании «Тойота» и в настоящее время с большим успехом применяется во многих про-мышленно развитых странах. Для обозначения этой системы в Японии применяется термин «канбан», означающий «карточка», или «визуальная система записи». Термин «ЛТ» является просто английским выражением, принятым в японских деловых кругах и, возможно, не имеющим японского эквивалента.
Суть системы JIT сводится к отказу от производства продукции крупными партиями. Взамен этого создаётся непрерывно-поточное предметное производство. При этом снабжение производственных цехов и участков осуществляется столь малыми партиями, что, по существу, превращается в поштучное. Данная система рассматривает наличие товарно-материальных запасов как зло, существование которого затрудняет решение многих проблем. Требуя значительных затрат на содержание, большие материальные запасы отрицательно сказываются на нехватке финансовых ресурсов, манёвренности и конкурентоспособности предприятия. С практической точки зрения главной целью системы ЛТ является уничтожение любых лишних расходов и эффективное использование производственного потенциала предприятия.
Система JIT является более увязанной со спросом, нежели традиционный метод «выбрасывания продукции на рынок». При этой системе действует принцип: производить продукцию только тогда, когда в ней нуждаются, и только в таком количестве, которое требуется потребителям. Спрос сопровождает продукцию через весь производственный процесс. При каждой операции производится только то, что требуется для следующей операции. Производственный процесс не начинается до тех пор, пока с места последующей операции не поступит сигнал о необходимости приступить к производству. Детали, узлы и материалы доставляются только к моменту их использования в производственном процессе.
Система JIT предусматривает уменьшение размера обрабатываемых партий, практическую ликвидацию незавершённого производства, сведение к минимуму объёма товарно-материальных запасов и выполнение производственных заказов не по месяцам и неделям, а по дням и даже по часам. В этих условиях упрощается система производственного учёта, так как появляется возможность осуществления учёта материалов и затрат на производство на одном объединённом счёте. Кроме того, при применении этой системы часть затрат предприятия из разряда косвенных переходит в разряд прямых. Например, в условиях организации производства по системе JIT рабочие производственных линий, занятые выпуском продукции, обязаны производить также техническое обслуживание, ремонт и наладочные работы, которые при традиционных условиях осуществляются другими рабочими и относятся к категории косвенных затрат. Это, в свою очередь, увеличивает точность исчисления себестоимости единицы продукции.
Управление стоимостью отличается от производственного учёта тем, что под этим в данном случае понимается регулирование уровня затрат независимо от того, имеют ли они непосредственное влияние на товарно-материальные запасы или финансовую отчётность, или нет. Применение принципов JIT упрощает процесс учёта производственных затрат и помогает менеджерам регулировать и контролировать расходы. Такое упрощение приводит к лучшему качеству производства, лучшему обслуживанию и лучшей оценке стоимости.
Традиционно система производственного учёта имеет тенденцию становиться всё более сложной с множеством счётно-учётных операций и отчётных данных. Упрощение же этого процесса преобразовывает систему производственного учёта в систему управления стоимостью. При системе учёта JIT учёт материалов и незавершённого производства ведётся на одном объединённом счёте. В этих условиях использование обособленного счёта для контроля за складскими запасами материалов теряет свою актуальность.
В условиях применения системы учёта JIT прямые затраты на оплату труда и заводские накладные расходы на счета производства не списываются. Прямой труд рассматривается как дополнительная часть общезаводских накладных расходов. Более того, сами заводские накладные расходы вместе с прямыми затратами оплаты труда списываются непосредственно на себестоимость реализованной продукции.
В традиционной бухгалтерии при организации закупок многими фирмами основное внимание уделяется учёту отклонений от цены приобретения материалов. Приемлемые отклонения от расчётной цены, как правило, достигаются за счёт приобретения большого количества материалов с соответствующими скидками или за счёт закупок низкого качества. В условиях же JIT основной упор делается на качество, доступность и общую стоимость операций, а не только на уровень закупочных цен.
На многих предприятиях с традиционной организацией производства большая часть усилий в области производственного учёта тратится на внедрение нормативов по трудозатратам и накладным расходам, а также на определение и учёт отклонений от этих нормативов. В компаниях же, работающих по системе JIT, отмечается снижение внимания к учёту отклонений по затратам на рабочую силу и накладным расходам. Даже те фирмы, которые по-прежнему используют анализ отклонений, подчёркивают, что переход на эту систему влечёт за собой изменение ракурса внимания. Использование анализа отклонений сохраняется на уровне предприятия, но основное внимание с позиций абсолютной значимости отклонений для каждого конкретного случая переходит на учёт вероятных тенденций развития производственного процесса.
Кроме того, традиционные показатели эффективности (как, например, выполнение норм выработки и коэффициент использования оборудования), являющиеся общепринятыми во многих системах производственного учёта, не вписываются в рамки принципов управления стоимостью в системе JIT. Причины такого несоответствия заключаются в следующем.
все эти показатели стимулируют формирование товарно-материаль-ных ценностей без учёта необходимых в режиме реального времени потребностей;
следование принципу оценки эффективности преимущественно по нормативным показателям ведёт к приоритету объёма производства над объёмом реализации и качеством продукции;
прямые трудовые затраты у большинства предприятий составляют от 5 до 15 \% от величины полных затрат на производство продукции;
применение коэффициентов использования оборудования является неприемлемым потому, что оно способствует завышению запасов товарно-материальных ценностей по сравнению с уровнем потребностей в них.
В заключение хочется отметить, что потенциальные преимущества системы JIT многочисленны. Во-первых, её применение приводит к уменьшению уровня запасов, что означает меньше вложений капитала в товарно-материальные запасы. Поскольку система требует иметь в наличии для немедленного использования минимальное количество материалов, то благодаря этому существенно снижается общий уровень запасов.
Во-вторых, в условиях применения системы JIT надёжность выполнения заказа намного возрастает, поскольку значительно меньше времени отводится на закупку и хранение материалов. Сокращение цикла выполнения заказа и возрастание уровня качества исполнения также способствуют существенному уменьшению потребности в резервном запасе, который представляет собой дополнительные учётные единицы запасов, служащие для предохранения от возможного дефицита. В этих условиях график производства в рамках планово-производственной перспективы также сокращается. Это позволяет выиграть время, необходимое для того, чтобы отреагировать на изменения конъюнктуры рынка. Производство продукции небольшими партиями благодаря ускоренному переходу в нормальное рабочее состояние способствует достижению большей гибкости.
В-третьих, при применении этой системы отмечается улучшение качества производства. Когда заказанное количество продукции невелико, источник проблем с качеством легко выявляется и коррективы вносятся немедленно. В этих условиях у работников многих фирм наблюдается большее понимание значения качества, что, в свою очередь, ведёт к улучшению качества производства на рабочих местах.
К другим преимуществам системы JIT можно отнести:
уменьшение капитальных затрат на содержание складских помещений для запасов материалов и готовой продукции;
снижение риска морального старения запасов;
снижение потерь от брака и уменьшение затрат на переделку;
уменьшение объёма документации;
снижение затрат на основные производственные материалы за счет повышения их качества.
Кроме того, система JIT воздействует на характер производственного учёта. В условиях её применения часть косвенных затрат переходит в разряд прямых. Такая трансформация понижает частоту использования носителей разнородных затрат для распределения затрат между видами продукции, тем самым увеличивая точность калькуляции затрат. По этой системе происходит преобразование производственного учёта в систему управления стоимостью, которая используется для обеспечения потребностей менеджеров в принятии эффективных управленческих решений о виде, цене, себестоимости, составе и путях сбыта продукции, способствуя дальнейшему совершенствованию производственной и коммерческой деятельности.
Выживание и эффективная деятельность предприятия в условиях рыночной экономики во многом определяются степенью развития управленческого учёта. И если финансовый учёт нацелен на соответствие отчётности предприятия внешним по отношению к компании требованиям и его формы регламентированы государством, то ведение управленческого учёта направлено на совершенствование управления бизнесом и методов его реализации предмет выбора топ-менеджеров организации.
Для обеспечения эффективного управления предприятием необходим интегрированный метод анализа и оптимизации затрат по всем статьям его деятельности. Такой метод управленческого учёта получил в экономической литературе название Cost Management (CM менеджмент затрат), при котором акцент был перенесён с подсчёта затрат на планирование и использование систем их учёта. Изменение взглядов на учёт в управлении был вполне естественной реакцией на глобальные изменения экономической системы, такие как бурное развитие информационных технологий, изменение характера производства, транснациональная конкуренция.
В 90-е гг. XX в. на основе общей теории СМ был разработан новый метод управленческого учёта Strategic Cost Analysis (SCA стратегический анализ затрат).
Стратегический анализ затрат важнейшая часть СМ, базирующаяся на термине value chain (цепь образования потребительной стоимости), который стал центральным объектом стратегического кост-менеджмента.
Согласно методу SCA деятельность фирмы трактуется как цепь образования потребительной стоимости (последовательность операций по созданию стоимости изделия). Каждое звено цепи рассматривается как с позиции её необходимости в производственном процессе, так и с позиции потребляемых ею ресурсов. Затем определяется cost driver (кост-драйвер) управляющий фактор, т.е. параметр, который характеризует стоимость выполнения конкретной операции. Путём контроля кост-драйверов и перестройки цепи образования стоимости предполагается достичь устойчивого преимущества над конкурентами.
Такое внимание специалистов в области SCA к работе предприятия в условиях острой конкуренции объясняет тот факт, что управленческий учёт в рамках этой теории фактически подчинён целям маркетинга. Если при традиционном ценообразовании за основу берётся себестоимость продукции и она воспринимается как данность, то практика целевой себестоимости исходит из маркетинговых оценок ёмкости рынка и конкурентоспособной цены. Исходя из объёма производства и розничной цены определяется целевая себестоимость. Задача стратегического анализа затрат конструирование такой цепи образования стоимости, чтобы реальная себестоимость не превышала целевую.
Таким образом, стратегия ценового лидерства предполагает поддержание того же качества продукции (услуг), что и у конкурентов, но при более низких затратах и, следовательно, ценах. Ценовое лидерство достигается за счёт экономии на объёмах производства, тщательного контроля затрат, минимизации затрат на этапах НИОКР, обслуживания, продаж и рекламы.
Помимо ценового лидерства SCA предусматривает такой фактор, как «уникальность», т.е. продукты «brand-name», дизайн, сервис.
Возможность следовать той или иной стратегии зависит от того, как фирма управляет своей цепочкой образования стоимости (ЦОС) по сравнению с конкурентами. Таким образом, анализ ЦОС необходим для определения того её сегмента, где могут быть снижены затраты либо повышена потребительная стоимость. Для достижения этой цели следует рассматривать ЦОС в масштабе не только одной фирмы, но и отрасли, т.е. учитывать процесс образования стоимости от добычи ресурсов до оказания сервисных услуг по ремонту готовой продукции. Такой масштаб позволит определить тот участок отраслевой ЦОС, где фирма потенциально может реализовать одну из своих стратегий и синхронизировать выбор своей стратегии с отраслевым окружением.
Именно рассмотрение отраслевой ЦОС отличает методологию стратегического анализа затрат (или стратегического управления затратами) от анализа в рамках традиционного управленческого учёта, областью которого являлась лишь технология добавления стоимости внутри фирмы.
Отраслевые показатели, оказывающие сильное влияние на рыночные предложения отдельных предприятий, в случае использования SCA успешно поддаются анализу и учёту.
Рассмотрим пример использования методов SCA в конкретной ситуации [6]. Компания производитель видеотехники решает снабдить модель видеомагнитофона самоочищающимися головками. С позиций традиционного управленческого учёта затраты на такое совершенствование считались бы неверными. Анализ с использованием ЦОС выглядит следующим образом. «Если магнитофон не имеет самоочищающихся головок, то пользователь должен будет потратить дополнительно 250 руб. в год на приобретение специальной чистящей кассеты. Средний срок эксплуатации составляет 4-5 лет, т.е. общие затраты составят не менее 1000 руб., не считая времени и неудобств. Затраты предприятия на установку самоочищающихся головок составят 100 руб. на единицу выпуска. Эта разница может быть перекрыта увеличением цены, так как экономия на ЦОС составит 900 руб.».
Таким образом, анализ затрат в рамках традиционного управленческого учёта зачастую оказывается неэффективным, так как недооцениваются внешние по отношению к предприятию звенья отраслевой ЦОС, что приводит к увеличению затрат и отрицанию выгодных решений.
Как же строится система стратегического анализа затрат на предприятии?
ЦОС разделяет отрасль на отдельные стратегические звенья, поэтому начальной точкой анализа затрат является определение ЦОС отрасли, отнесение затрат, доходов и активов к различным её звеньям. Затем устанавливаются факторы, от которых зависят затраты на каждом звене ЦОС кост-драйверы. И наконец, формируется система действий, в результате которых фирма может получить конкурентные преимущества.
Звенья отраслевой ЦОС это основные массивы затрат в бизнес-процессах, например, закупка сырья, транспортировка и другое (естественно, для каждой отрасли они различны). Кост-драйверы для каждого звена ЦОС также выделяются отдельно.
Диагностика кост-драйверов для понимания характера затрат в каждом звене второй шаг в создании и анализе ЦОС. В отличие от традиционного управленческого учёта, где единственным кост-драйвером считается объём выпуска, в стратегическом анализе затрат рассматриваются структурные и операционные виды кост-драйверов.
Структурные кост-драйверы определяются особенностями экономической политики компании. SCA предлагает пять критериев для выбора структурных кост-драйверов:
масштаб производства, определяющий объём инвестиций в производство, НИОКР, маркетинг;
охват — степень вертикальной интеграции;
экономический опыт осуществления предполагаемых операций;
технологии и их специфика;
- сложность — широта номенклатуры продукции (услуг). Операционные кост-драйверы характеризуют способность фирмы успешно
реализовывать свою структурную политику. Перечень основных операционных кост-драйверов содержит:
вовлечение персонала в достижение общих целей фирмы;
всеобщее управление качеством (TQM — Total Quality Management), основанное на следующих принципах: принятие решений на фактах; системный и процессный подход; лидерство руководителя; вовлечение в процессы улучшения качества всего персонала и т.п;
уровень загрузки мощностей;
эффективность расположения мощностей;
конструкция изделий;
связи с поставщиками и потребителями.
Третий шаг в анализе ЦОС — создание устойчивого конкурентного преимущества. Для каждого звена ЦОС формулируются два ключевых вопроса: могут ли быть снижены затраты на звено при том же уровне потребительной стоимости (дохода); может ли быть увеличена потребительная стоимость (доход) без увеличения затрат.
Таким образом, задача состоит в лучшем контроле затрат, чем у конкурента, или в реорганизации ЦОС для получения большей потребительной стоимости.
Метод SCA может предоставлять информацию для стратегических решений по таким вопросам, как оценка затрат по изменению атрибутов изделий и измерение стоимости «барьеров», которые необходимо преодолеть конкурентам для создания устойчивого конкурентного преимущества (объём инвестиций).
Стратегический анализ затрат в части разработки и оценки ЦОС тесно связан с техникой учёта и спецификой конкретного предприятия и требует профессиональной оценки и анализа его деятельности.
Достаточно новым методом анализа затрат на качество является бенч-маркинг [4].
Бенчмаркинг представляет собой искусство обнаружения того, что другие делают лучше, т. е. это постоянный процесс изучения и оценки товаров и услуг, опыта производства лучших своих конкурентов либо тех предприятий, которые стали признанными лидерами в своих областях. Родиной данного понятия является США. Впервые бенчмаркинг появился в 1972 г. в Институте стратегического планирования Кембриджа. Исследовательско-консалтинговая компания «Pims» установила, что для нахождения эффективного решения в условиях конкуренции необходимо изучать и использовать опыт других предприятий, которые имеют успех в родственных областях. В 1979 г. американская компания «Xerox» приступила к проекту «Бенчмаркинг конкурентоспособности» для анализа качества собственной продукции и затрат, связанных с производством, по сравнению с результатами японских производителей. С тех пор к бенчмар-кингу стали относиться с доверием. Однако для большинства компаний бен-чмаркинг не является новым инструментом экономики качества. Он осуществляется в рамках конкурентного анализа, хотя бенчмаркинг является более детализированной, формализованной и упорядоченной функцией, чем метод или подход конкурентного анализа. Это необходимый институт для достижения успеха любой организации.
Бенчмаркинг позволяет осуществлять следующие процессы:
непрерывное улучшение всех процессов жизненного цикла продукции;
определение областей, в которых улучшение качества принесёт наиболее значимые результаты по ключевым вопросам бизнеса или отношений с заказчиком;
установление стандартов там, где накоплен и определён наилучший опыт;
определение лучших организаций, придерживающихся данных стандартов;
адаптация и применение полученных от таких подходов методов и опыта с целью проведения бизнеса в соответствии со стандартами и получения превосходства над конкурентами.
В настоящее время бенчмаркинг становится искусством обнаружения того, что другие компании делают лучше: изучение, усовершенствование и применение их методов работы на собственных компаниях.
Определяя эффект, который может обеспечить бенчмаркинг, следует иметь в виду, что никогда и никем не подвергался сомнению факт выгодности обмена опытом и его изучения. Правда, не следует забывать, что и «перекрёстное опыление» плодотворно не для всякого предприятия. Поэтому необходимость проведения бенчмаркинга должна быть доказана.
Таким образом, польза бенчмаркинга состоит в том, что производственные и маркетинговые функции становятся наиболее управляемыми, когда исследуются и внедряются лучшие методы и технологии других предприятий или отраслей. Это может привести к прибыльному предпринимательству с высокой экономичностью, созданию полезной конкуренции и удовлетворению потребностей покупателей.
Процесс эволюции бенчмаркинга аналогичен классической модели «перехода от искусства к науке».
Первое поколение бенчмаркинга интерпретируется как реинжиниринг или ретроспективный анализ товара.
Второе поколение — бенчмаркинг конкурентоспособности — развивается как наука в 1976 — 1986 гг. благодаря деятельности фирмы «Ксерокс».
Третье поколение бенчмаркинга развивается в период 1982 — 1986 гг., когда предприятия-лидеры качества выясняют возможность поучиться у предприятий вне их сектора или отрасли, а не у своих конкурентов.
Четвёртое поколение бенчмаркинга это стратегический бенчмаркинг, который рассматривается как систематический процесс, направленный на оценку альтернатив, реализацию стратегий и усовершенствование характеристик производительности на основе изучения успешных стратегий внешних предприятий партнёров.
Пятое поколение глобальный бенчмаркинг рассматривается будущим инструментом организации международных обменов с учётом культуры и национальных процессов организации производства. Таким образом появилось новое направление в менеджменте кросскультурный менеджмент, заключающийся в сравнении методов и принципов управления, т.е. менеджменте на стыке деловых культур.
Основа философии бенчмаркинга.
знание процессов, выполняемых в организации;
знание лидеров в своей области;
использование лучшего опыта лидеров в работе своей организации;
получение прибыли от внедрения превосходных практик.
Знание процессов, выполняемых в организации, в первую очередь предполагает анализ текущих процессов организации, оценку их сильных и слабых сторон, документирование выполняемых процессов, представление процессов на картах и диаграммах, измерение параметров процессов, изучение требований потребителей. Знание лидеров в своей области предполагает установление главных конкурентов, их сильных и слабых сторон для понимания того, как лучше соревноваться с ними. Прежде всего необходимо учиться у организаций, имеющих мировой класс. Включение всего лучшего в работу организации означает восприятие и адаптацию лучших практик. Получение прибыли от превосходства это использование «лучшей из лучших» практик в организации, совершение прорыва за счёт этого в своей области и достижение уровня исполнителя мирового класса. В зависимости от целей организации и от её ресурсов размер прибыли от использования практики превосходства может быть разным.
Бенчмаркинг охватывает очень широкий спектр вопросов от политики организации, её стратегии, удовлетворения запросов потребителей до различных процессов и функций, выполняемых в организации.
В зависимости от того, проводится бенчмаркинг внутри организации или сравниваются родственные организации, различают внутренний или внешний бенчмаркинг.
Внутренний бенчмаркинг предполагает сравнение однородных объектов внутри организации. В зависимости от объекта сравнения существуют различные виды внутреннего бенчмаркинга. Бенчмаркинг процессов сравнение однородных процессов, протекающих параллельно.
Бенчмаркинг характеристик процессов сравнение характеристик однородных процессов. Бенчмаркинг функций сравнение однородных функций, являющихся составной частью как однородных, так и разнородных по своей природе процессов. Бенчмаркинг затрат сравнение затрат, связанных с любым этапом выполнения процесса, или общих затрат, связанных с выпуском продукции или предоставлением услуг.
Бенчмаркинг продукции (услуг) сравнение различных видов продукции (услуг), предлагаемых организацией, либо с точки зрения самой организации, либо с точки зрения потребителя. Бенчмаркинг потребителя сравнение различных потребителей продукции или услуг одной организации.
Внешний бенчмаркинг в зависимости от того, «с кем сравнивают», подразделяют на бенчмаркинг конкурентоспособности, функциональный бенчмар-кинг, стратегический и глобальный. В свою очередь, объектами сравнения внешнего бенчмаркинга также могут являться процессы, характеристики процессов, функции, затраты, потребители, продукция. Однако основным объектом бенчмаркинга следует признать процесс или его функции, так как все остальные объекты: продукция, затраты, удовлетворённость потребителей являются результатом процесса. Поэтому мы рассмотрим бенчмаркинг процессов и функций. Бенчмаркинг может применяться к процессам разного уровня.
Согласно прагматической аксиоме Деминга любую деятельность, в том числе работу организации, необходимо рассматривать как технологический процесс. Процесс это система действий, которая использует ресурсы для преобразования входящих элементов в выходящие. Выделяют следующие элементы процесса. Входящие элементы это продукция, услуги, предоставляемые поставщиками, что делает возможным выполнение процесса. Например, информация, материалы, комплектующие.
Выходные элементы это результаты процесса, в первую очередь продукция, в том числе услуги.
Потребитель (заказчик) организация или лицо, ради которого осуществляется процесс и выпускается продукция или предоставляется услуга.
Требования заказчика это установленные или ожидаемые его потребности.
Обратная связь система получения информации об удовлетворённости потребителей и использование этой информации в процессе повышения удовлетворённости. Организация система, имеющая особые задачи и свою структуру.
Ключевой процесс это процесс, выполняемый в функционально различных пространствах организации и являющийся главным, с точки зрения удовлетворения потребителей, а также результатов бизнеса самой организации.
Функциональный процесс часть ключевого процесса, полностью выполняемая в пределах одного функционального пространства.
Субпроцесс законченная часть функционального процесса.
Процесс бенчмаркинга может включать четыре фазы, разбитые на десять этапов.
Фаза планирования.
Установление объекта бенчмаркинга, а именно процесса, который предлагается улучшить. Определение области деятельности организации, где самые большие возможности для улучшения. Документирование текущего процесса. Разработка описания проекта.
Установление конкурента по бенчмаркингу. Определение того, кто применяет «превосходную» практику в той области, которая интересует организацию.
Планирование и проведение наблюдений «превосходной практики». Выполнение наблюдения за «превосходной» практикой непосредственно у конкурента по бенчмаркингу.
^Аналитическая фаза.
Определение текущего уровня выполнения процесса. Проведение анализа текущего выполнения процесса.
Проектирование будущего уровня выполнения процесса. Выявление тенденций отрасли и определение того, каким образом можно достичь преимущества.
Фаза интеграции.
Анализ результатов бенчмаркинговых исследований в организации. Анализ предполагаемых результатов бенчмаркинговых исследований на всех уровнях организации, достижение согласия.
Пересмотр установленных целей и оперативных планов, доведение до сведения всех заинтересованных лиц об этих изменениях.
Фаза действий.
Разработка плана мероприятий. Разработка специальных мероприятий, системы измерений и расписания для внедрения новых практик, найденных в результате бенчмаркинга.
Осуществление прорыва. Выполнение плана мероприятий, необходимость которых установлена в результате бенчмаркинга, осуществление мониторинга результатов.
10. Повторение процесса. Удержание текущего выполнения процесса на
уровне ведущего для отрасли.
Таким образом, применение бенчмаркинга позволит организации: опираться на успех других организаций; учитывать современный опыт, а не устаревшие идеи; значительно снизить издержки от повторной работы, дублирования; улучшить понимание того, что делается и насколько эффективно осуществляется деятельность; организовывать более эффективно управление; ставить реальные цели; определить необходимые изменения; усилить ответственность сотрудников.
Рассмотренные методы анализа затрат на качество являются средствами их минимизации, позволяющими высвобождать капитал и направлять его на освоение новых направлений деятельности и, как следствие, выходить организациям на новый, более качественный уровень развития.
Обсуждение Экономика качества
Комментарии, рецензии и отзывы